Solution
Saving energy by modification of an existing constant speed centrifugal chiller to include variable speed drive capability
Mitsubishi Heavy Industries Thermal Systems (MHI Thermal Systems) provides a solution that improves the energy-saving performance of constant speed centrifugal chillers that are already installed. The modification to a variable speed drive improves the compressor‘s controllability and its cooling efficiency especially when outside is cold and cooling water entering temperature become low. We propose a centrifugal chiller and cooling system that meets the increasing need for energy-saving to reduce environmental impact and can maintain high-efficiency operations over a long period of time.
FEATURES
Variable speed drive improves part load COPs
Constant Speed centrifugal chillers' cooling water entering temperature has a rated value, and the chiller attains highest Coefficient Of Performance (COP) when it operates under those rated conditions. However, when viewed throughout the year, operation at rated conditions in standard factories, commercial facilities, and office buildings is only for a short period, and is mostly under part load or low cooling water temperature conditions. The modification of an existing constant speed centrifugal chiller to a variable speed drive can significantly improve the COP under part loads by regulating the motor speed according to cooling demand needed and cooling water entering temperature. MHI Thermal Systems has been developing compressor design technology and control technology of variable speed drive over many years, and these can be used to enable stable control at low cooling water entering temperatures. This means that in addition to winter months, it can significantly lower nighttime power consumption and contribute to energy cost reduction in regions with large temperature differences such as the Middle East, along with tropical regions such as Southeast Asia where there is little seasonal variation.
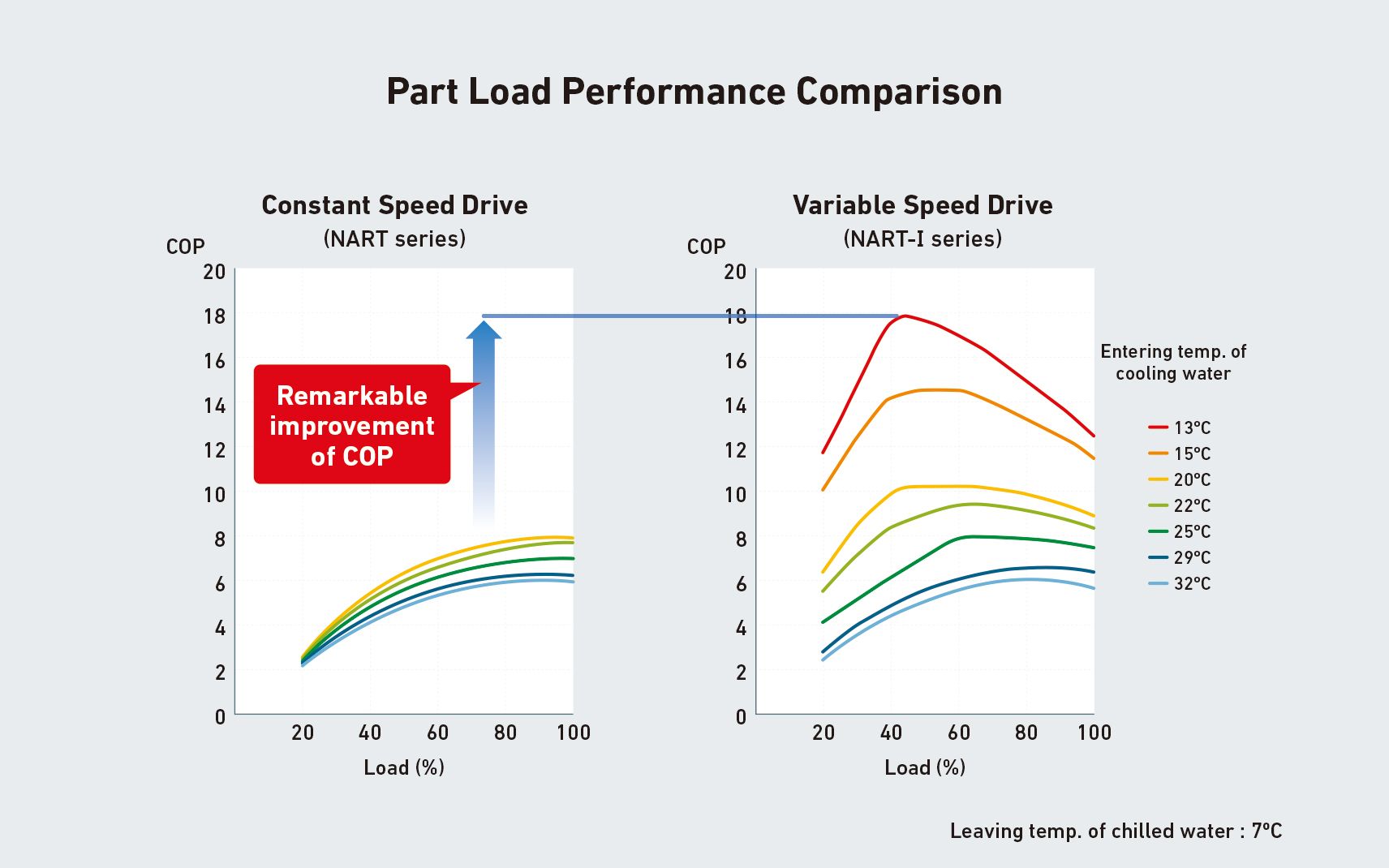
Optimized control makes operations more efficient
For a centrifugal compressor of chiller, inlet guide vane control and hot gas bypass valve control are applied for the purpose of load control. However, in general, the inlet guide vane control increases resistive loss when its opening ratio is low, therefore, it is preferable to control the inlet guide vane at higher opening ratio as much as possible. In addition, since the hot gas bypass valve control used in low load range causes loss on the refrigeration cycle, it is preferable to control the hot gas bypass valve opening as small as possible. With the variable speed control designed in consideration of these points, a control map as shown below has been realized, the performance degradation is minimized in the entire range of operation, and high efficient operation has been achieved over a wide load range.
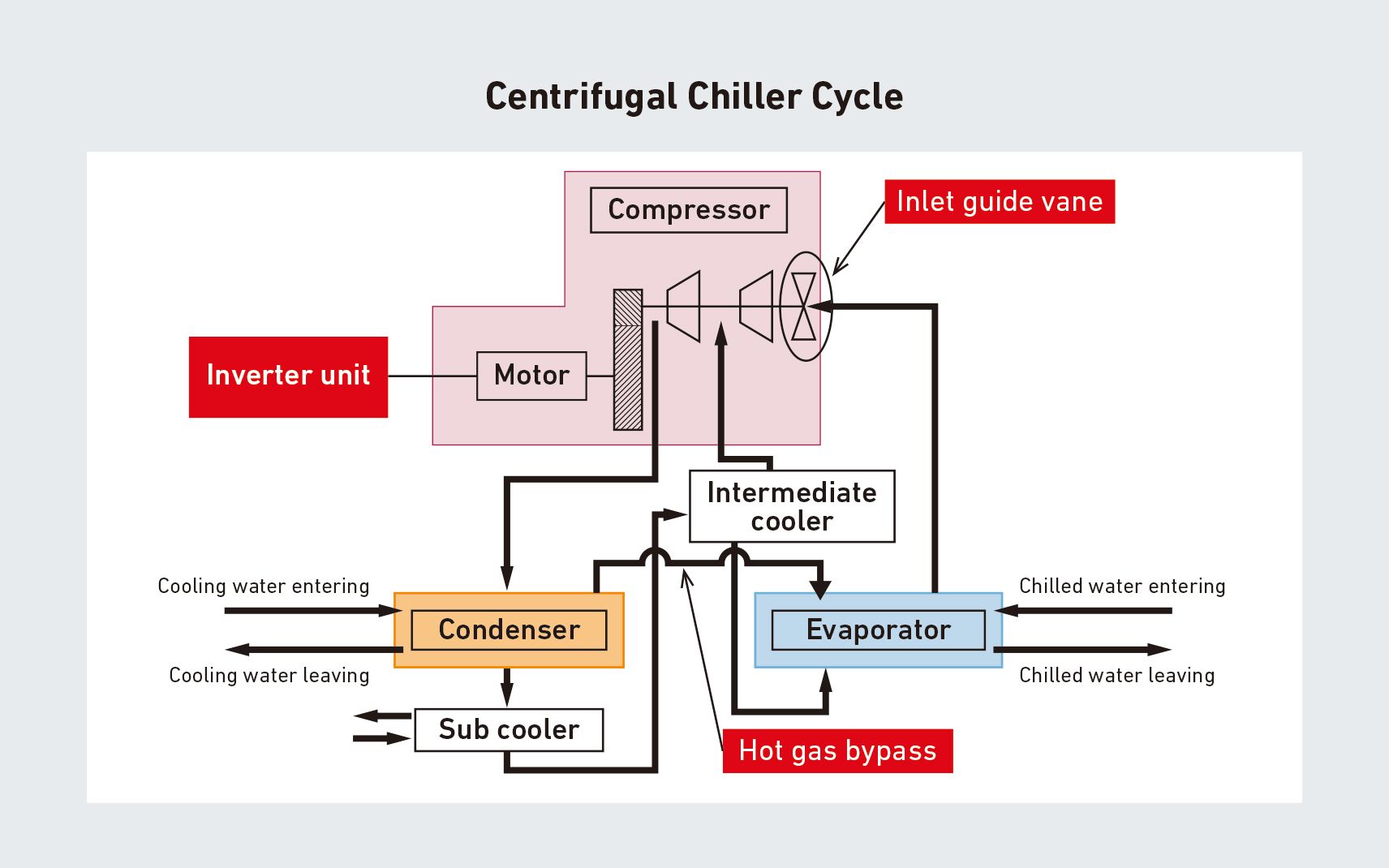
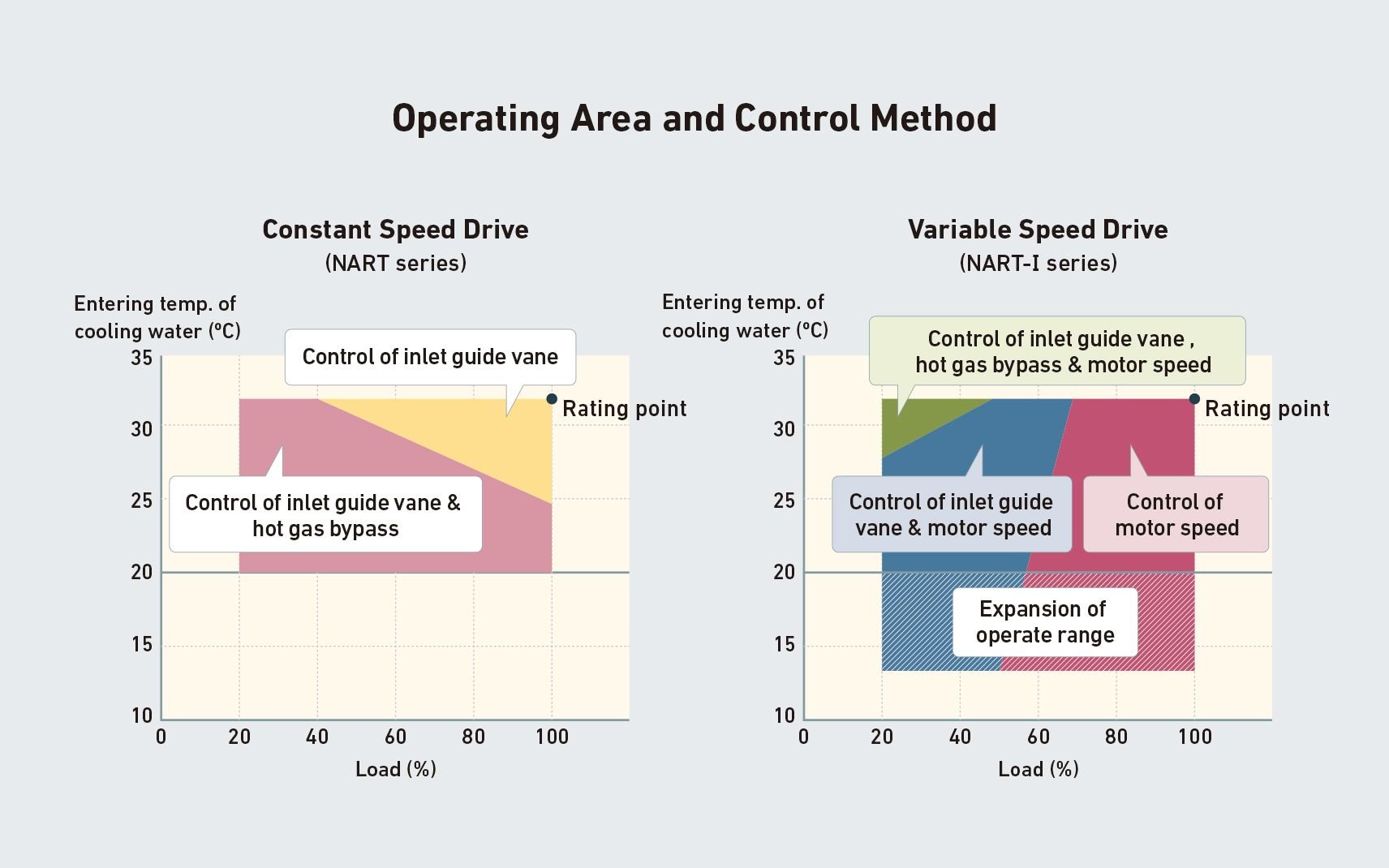
Upgrading existing centrifugal chillers to be more energy efficient
MHI Thermal Systems has delivered a number of centrifugal chillers such as for district heating and cooling, factory air conditioning systems, and other applications, and has the top market share of the Japanese market in this field. While the company has been developing and delivering energy efficient and lower environmental impact centrifugal chillers, the company also hears customer needs and supports upgrading existing centrifugal chillers to be more energy efficient; it is possible to add a Variable Speed Drive Capability to an existing Constant Speed Centrifugal chillers that have been installed for more than 10 years, bringing them closer to the latest chiller efficiency.