Case study
Industry: Power generation, Steelmaking, Cement, Oil & Gas
ISSUE
Decarbonizing hard to abate sectors
As governments around the world set increasingly ambitious targets for reducing CO₂ emissions, the transition to a low carbon or zero carbon economy has become a pressing issue for industry. In particular, emission-intensive industries such as coal-fired power generation, steelmaking, cement, and liquefied natural gas production facility need to implement concrete objectives for reducing emissions.
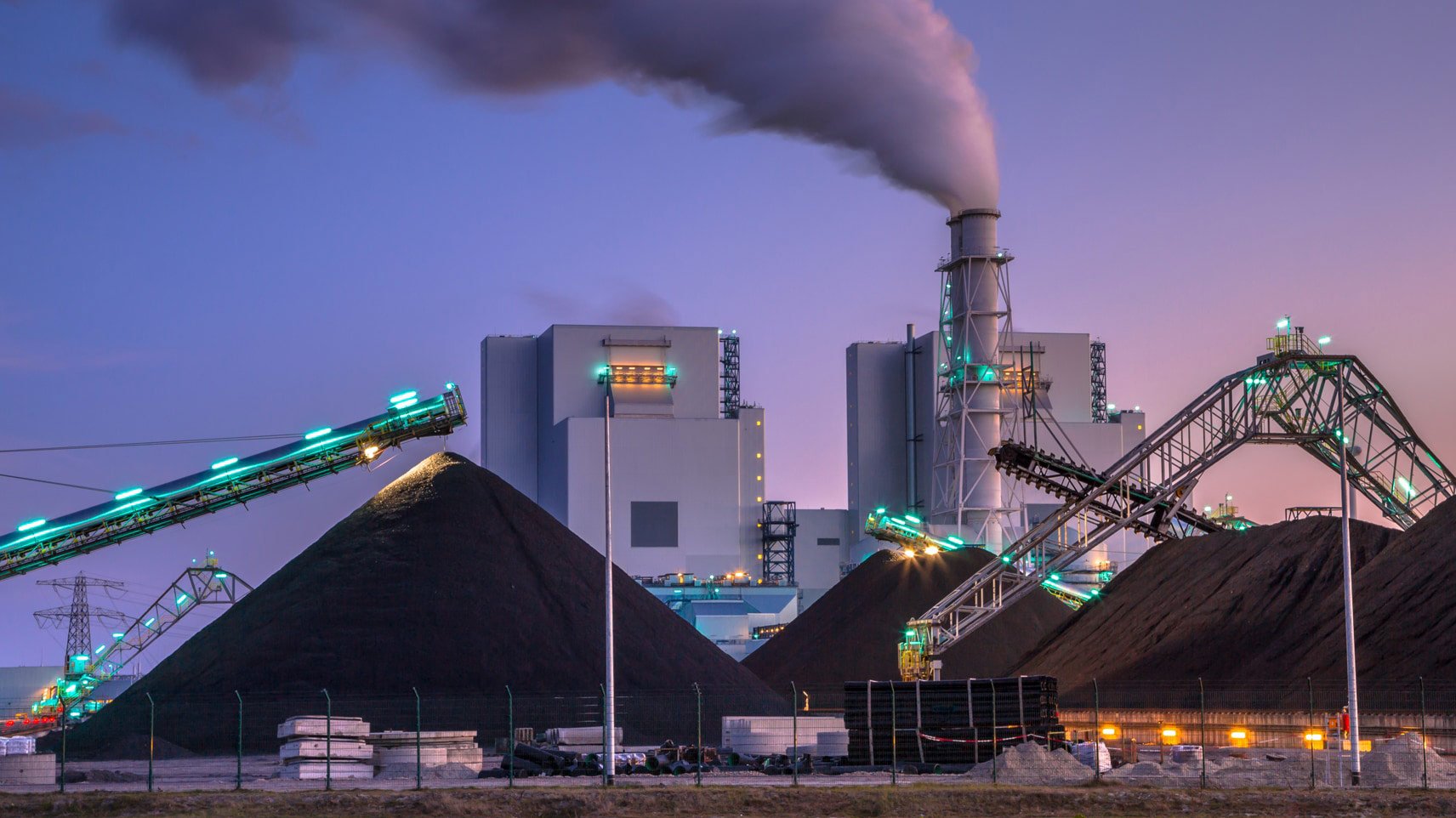
Emissions goals create demand for cheaper carbon capture technology
Right now, industries are considering how to reduce their carbon footprints by boosting efficiency or switching to electrification and low-carbon fuels. While carbon capture is another option for removing emissions that cannot be eliminated by these means, recovery costs account for over 60% of the costs associated with the CO₂ value chain. Consequentially, carbon capture plants need to become more economical.
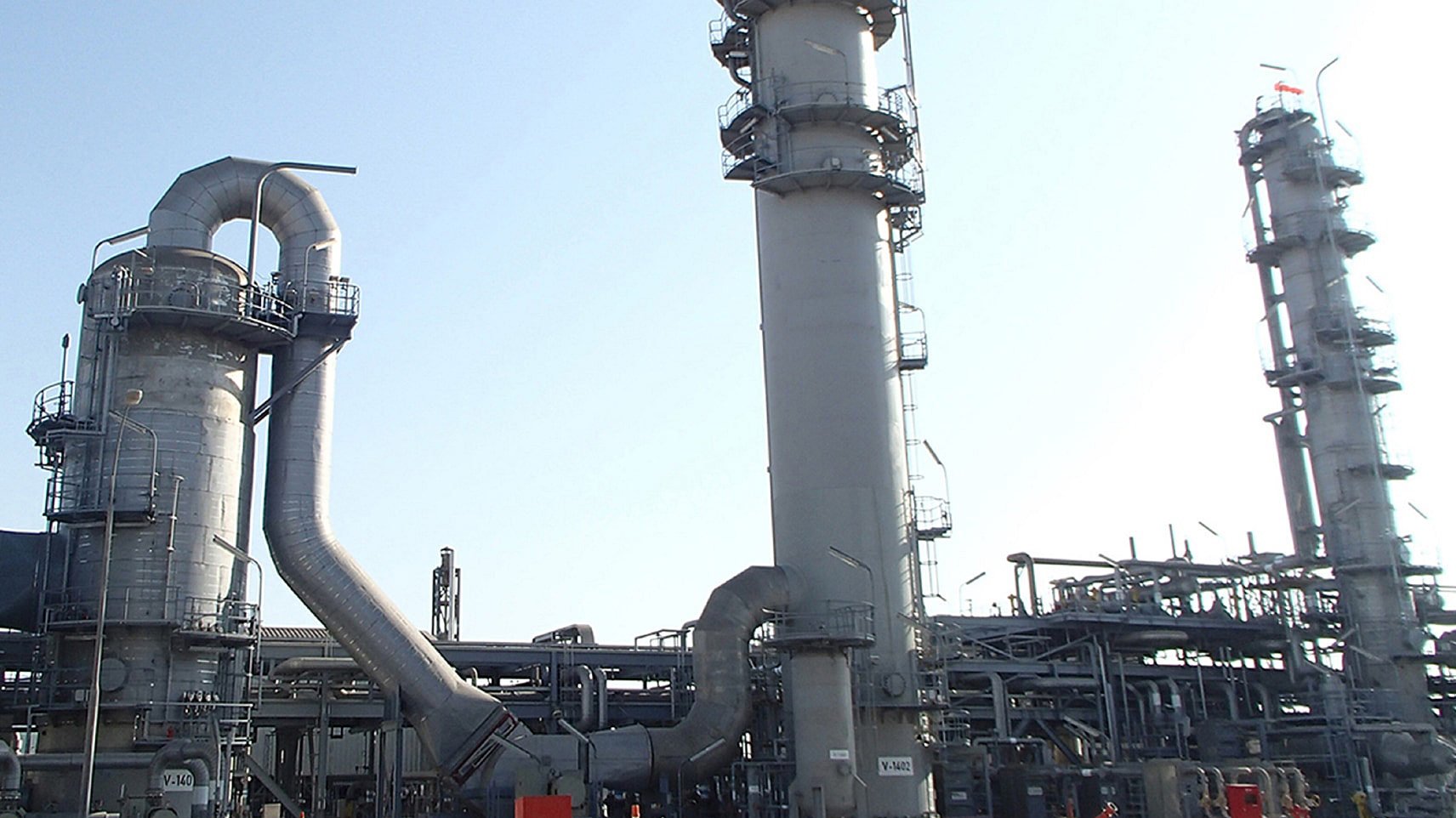
SOLUTION
KEY POINTS TO THE SOLUTION
- Compact, modular systems to reduce capital expenditure
- Automated operation and remote service through DX to reduce operating expenditure
Compact, modular systems reduce capital expenditure
Mitsubishi Heavy Industries reduces capital expenditure associated with CO₂ compressors for carbon capture and storage (CCS) applications by making ancillary equipment more compact and employing a modular design that integrates compressors and associated systems. The modular approach to installation enables operations to save time and costs on site.
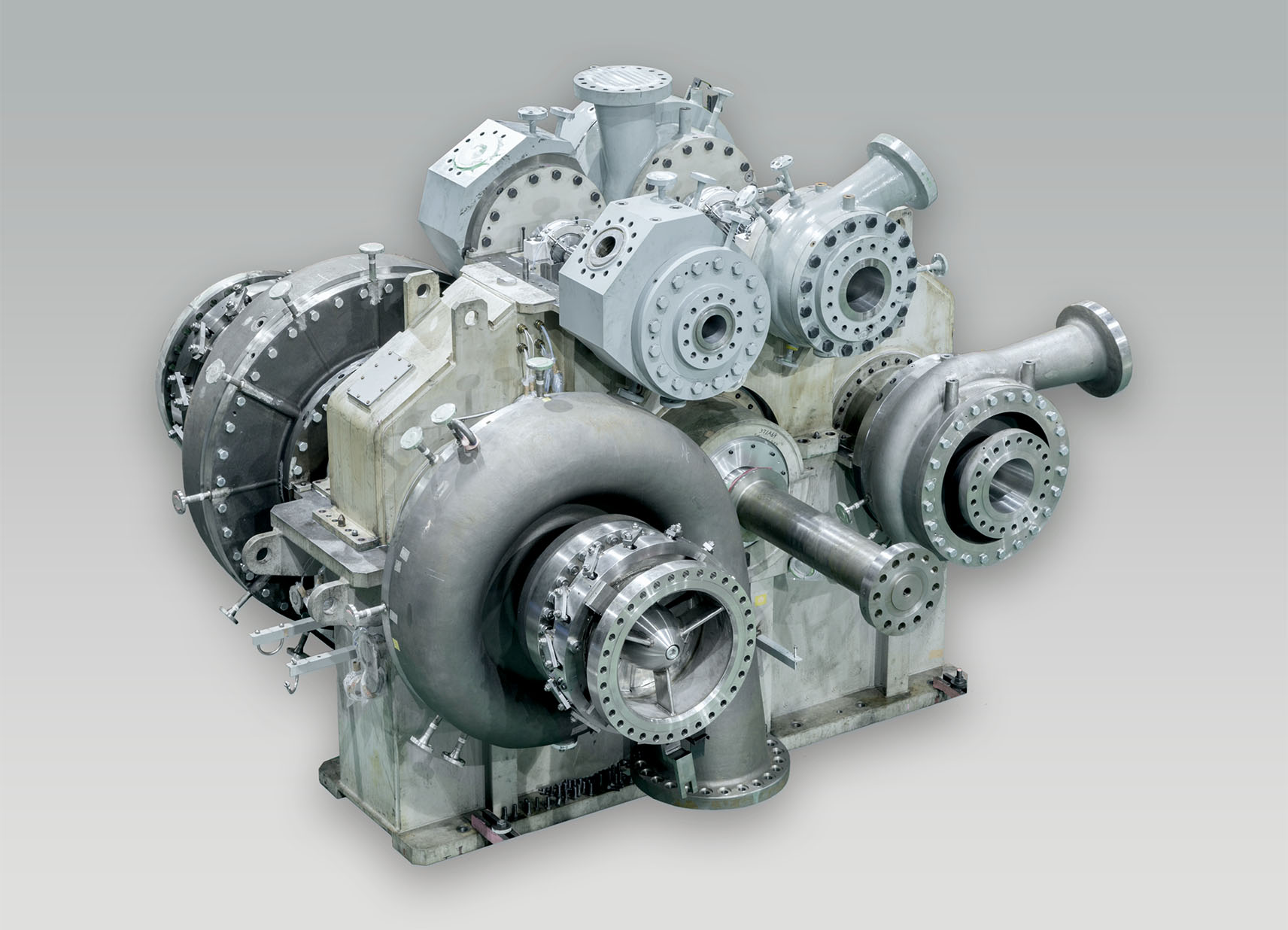
Automation and remote service through DX reduce operating expenditure
MHI enables monitoring by remote service of compressor operations, using artificial intelligence to establish optimum operating conditions. In the unlikely event of a malfunction, the system displays guidance on what action to take. The system enables operators to better visualize plant status and is able to propose an optimized maintenance schedule, thereby reducing maintenance costs.
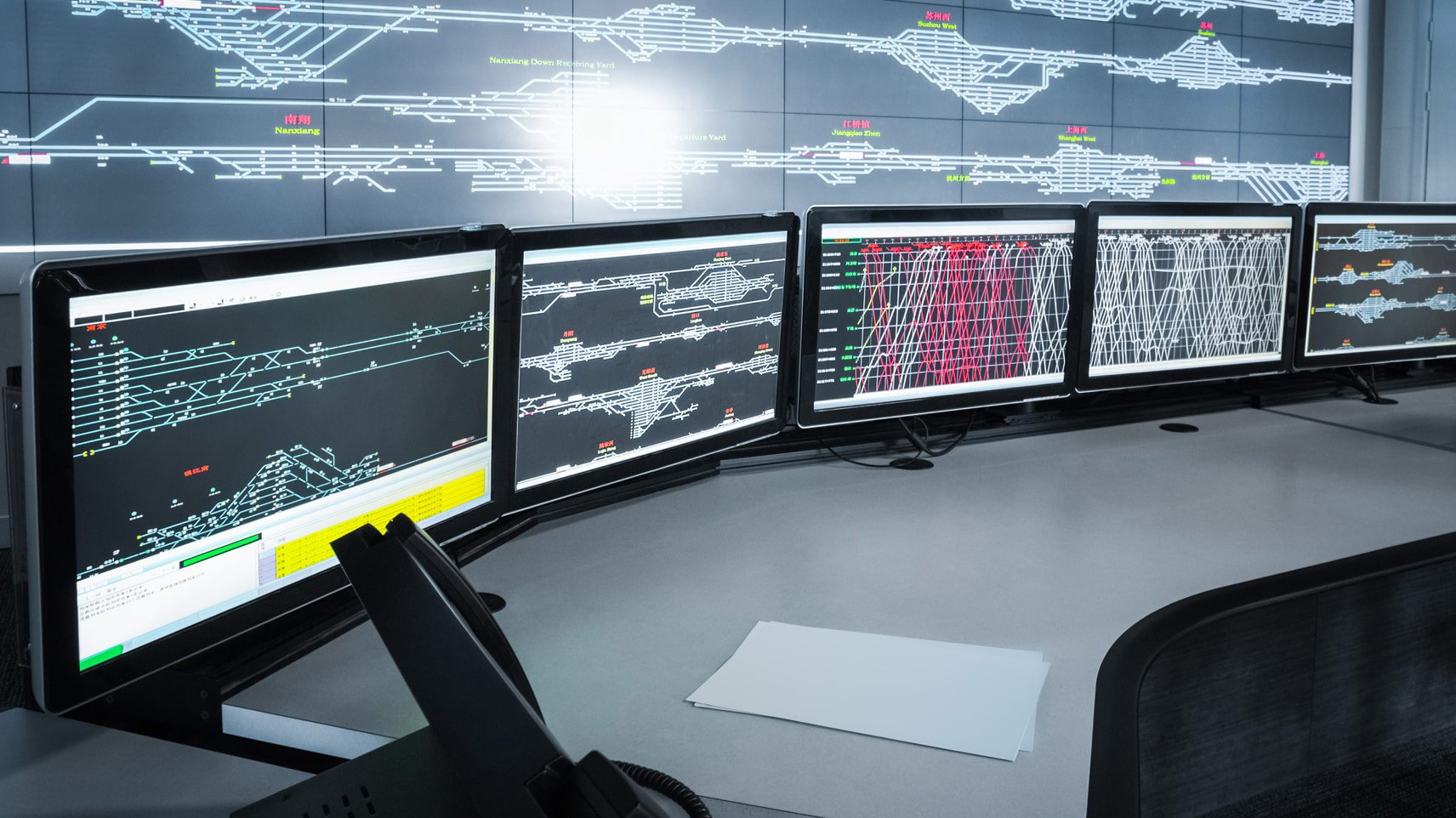
EXPECTED OUTCOME
- Based on our experience of installing one of the world’s largest CO₂ recovery compressors (rated at 5,000 TPD) at the Petra Nova Carbon Capture project in the US in 2015, we are able to reduce the risk of compressor stoppages, thereby ensuring a more stable operation.
- The modularization of compressors and ancillary equipment enables operators to reduce capital expenditure.
- By enabling operators to better visualize plant status, the MHI system is able to propose an optimized maintenance schedule, thereby reducing maintenance costs.