Case study
Industry: Manufacturing
ISSUE
Recurrence of chiller shutdowns must be prevented
In periodic inspection on a centrifugal chiller in Asia that went into service in 2018, an alarm indicating a low inflow rate of cooling water was observed. Failure data of liquid terminal temperature difference (LTD) was then detected in the condenser. Together with the local services company, Mitsubishi Heavy Industries Thermal Systems (MHI Thermal Systems) proposed cleaning the condenser, but several months ended up passing without it actually being done. Then, the chiller shut down (tripped). Countermeasure will now be needed to prevent the recurrence of chiller shut down in the future.
SOLUTION
KEY POINTS TO THE SOLUTION
- Identify causes of chiller shut down and promptly resolve troubles
- Acknowledge importance of monitoring operating condition by the concerned parties and reinforce the monitoring to prevent recurrence
- Provide periodic inspection to prevent forced shut down and experienced maintenance to reduce energy loss
Identify causes of chiller shut down and promptly resolve troubles
The shut down that occurred in this instance was caused by condenser pressure reaching its limit due to Liquid terminal temperature difference (LTD) increase caused by slime deposits on the inner surfaces of the condenser cooling water tubes. We finished brush cleaning the condensers and resolved the trouble four days after the shut down occurred. Foaming was also confirmed in water tanks at the cooling tower site and an increase in the density of microbial contaminants in the circulating cooling water was identified as a potential root cause of the problem. We recommend chemical cleaning. Cleaning the condenser tube improved the efficiency of the chiller which had become less efficient of heat transfer due to contamination on the inside. The following graph shows periodic inspection data and trend curve around tube cleaning. After cleaning the condenser tube, much heat was transferred to the cooling water. Liquid terminal temperature difference (LTD) which is an indicator of tube dirty has improved after cleaning. Efficiency of heat transfer was improved by approx. 30%, and energy loss was also improved accordingly.
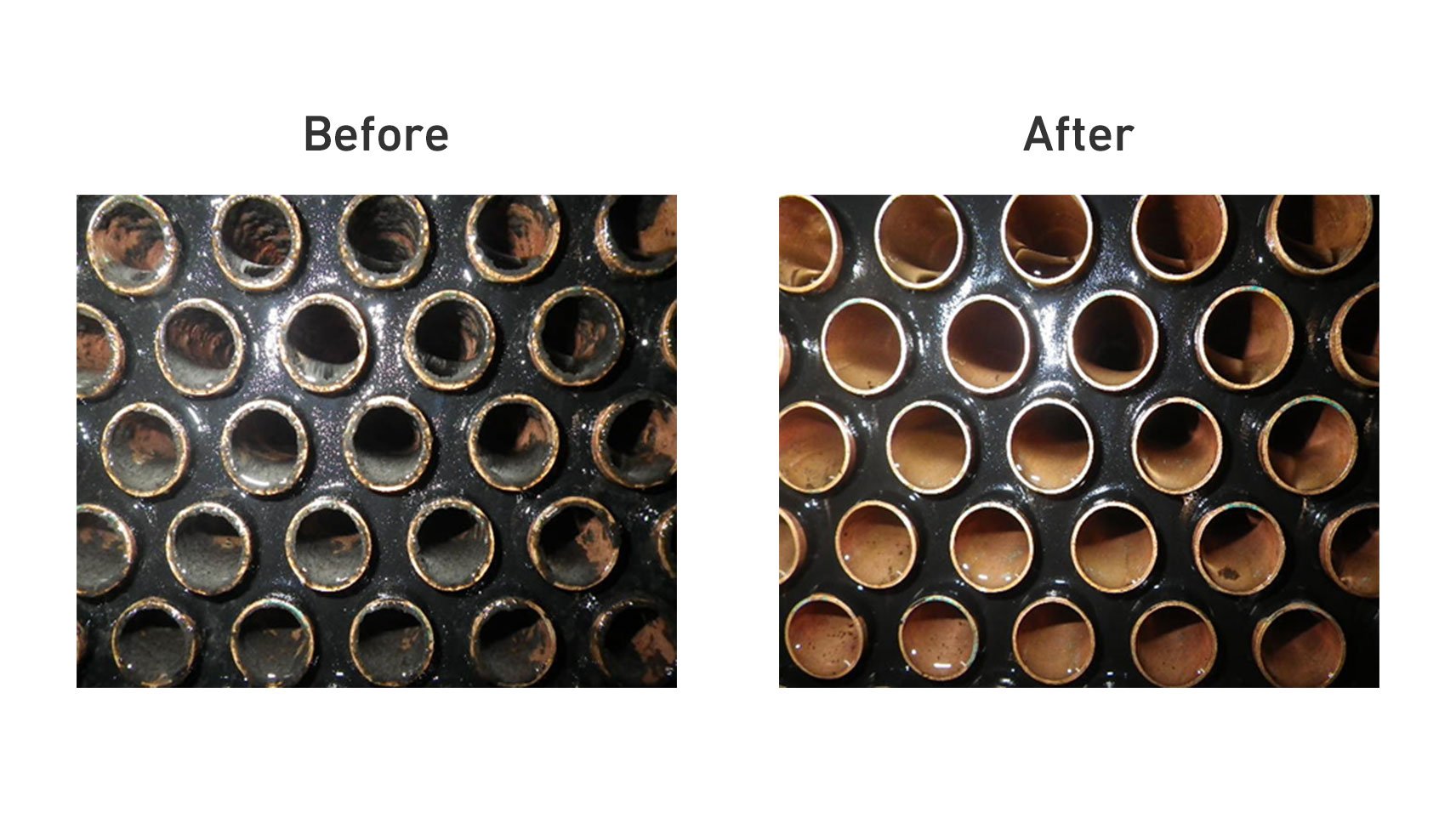
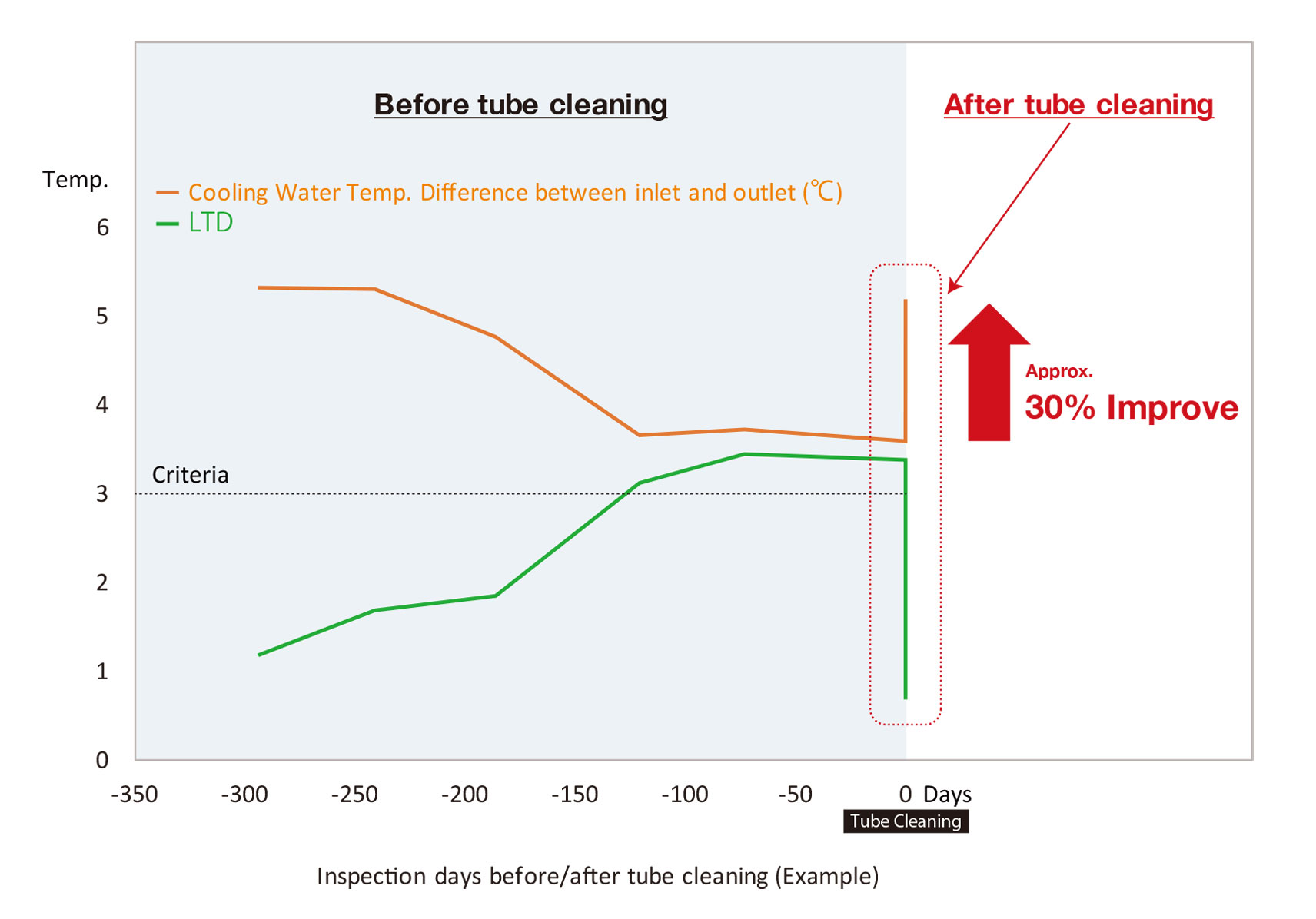
Acknowledge importance of monitoring operating condition by the concerned parties and reinforce the monitoring to prevent recurrence
Aside from condenser pressure reaching its limit, it was also confirmed by re-examining historical data that the cooling tower inlet and outlet water temperature difference was gradually decreased and the criteria for condenser liquid terminal temperature difference (LTD) had been exceeded. We reaffirmed together with the customer and the local services partner how important continuous monitoring and appropriate maintenance are as countermeasures for preventing recurrence of forced shut down .
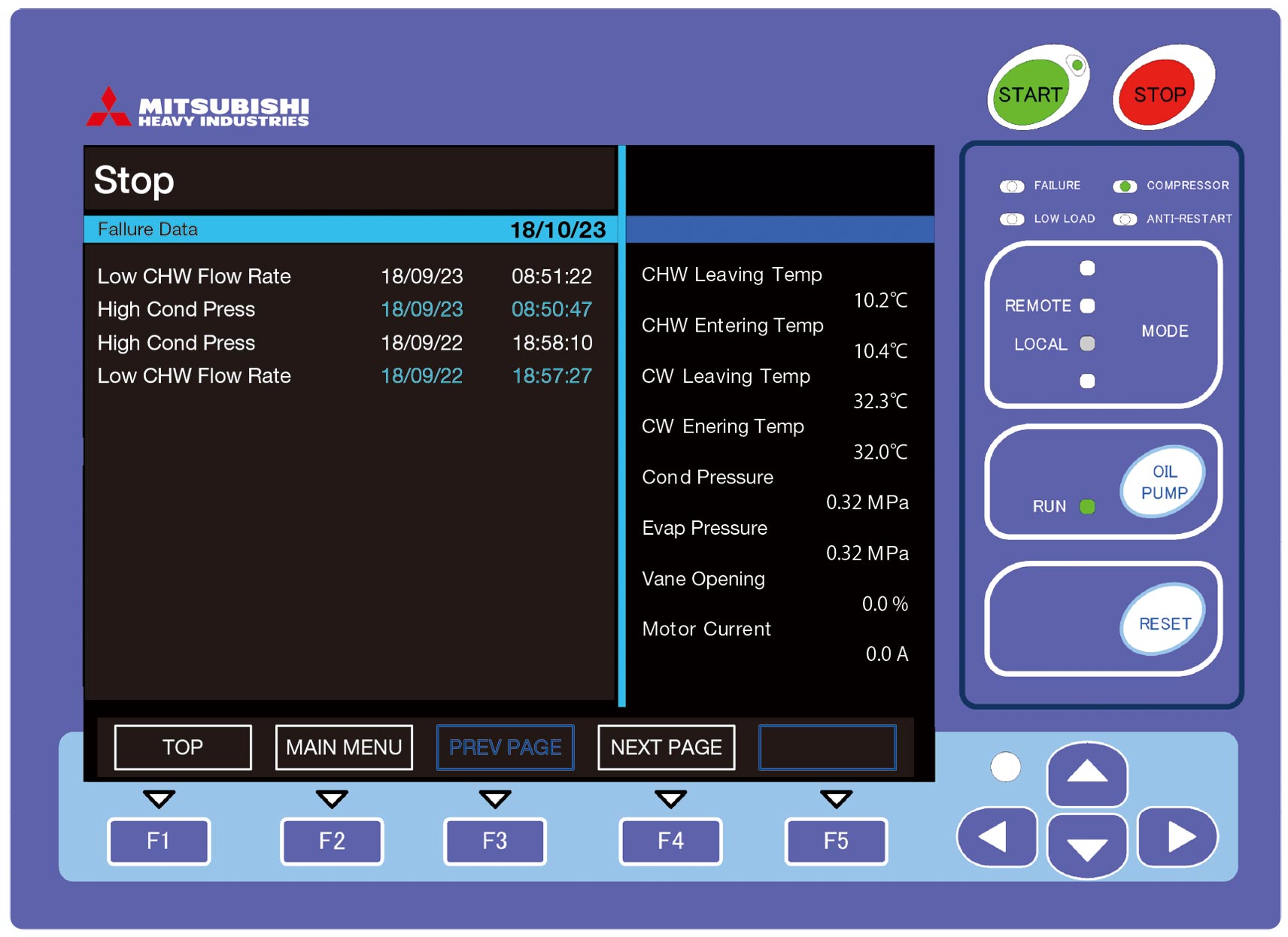
Provide periodic inspection to prevent forced shut down and experienced maintenance to reduce energy loss
As specific countermeasure against shut down recurrence, MHI Thermal Systems proposed a robust time-based maintenance program that includes continuing on-site inspections and conducting eddy current testing (ECT) on condenser tubes. To strengthen cooperation with the customer and the local services partner, we are sharing data and information with them so that all parties are able to regularly and timely understand the real condition of the chiller. For example, we are able to visualize the energy performance of chiller and main heat exchangers by analyzing the various data obtained from monitoring systems. With such analyzed date and information, we also can offer to the management of the customer for their decision-making whether they implement the necessary countermeasures against potential trouble for optimal operations. Our comprehensive services support more economical chiller operations for the customer.
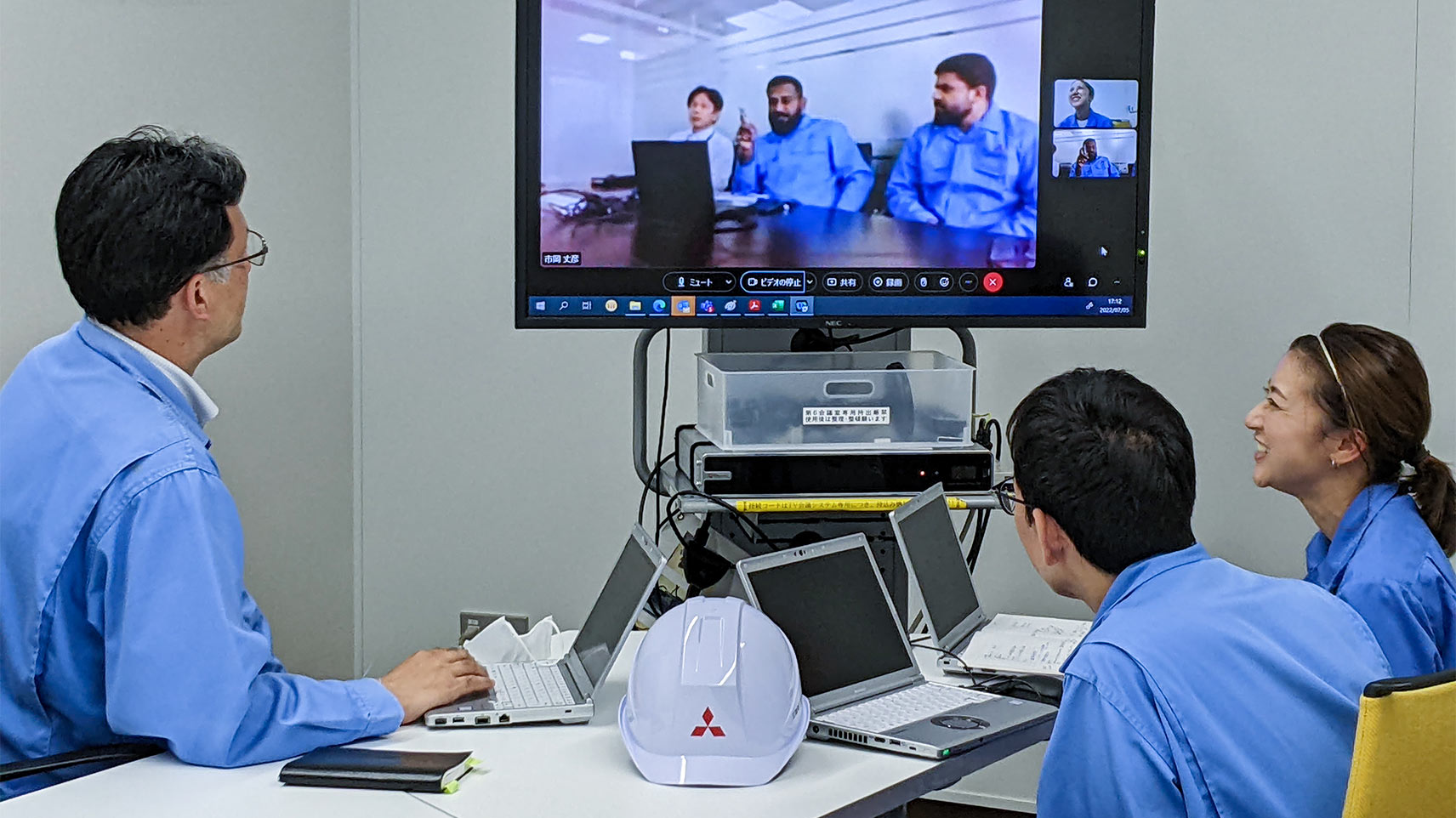
EXPECTED OUTCOME
- Prevent forced shut down of the chiller before it occurs
- Analyze root causes of trouble in detail and prevent recurrence
- Operate economically the chiller with reduced energy loss by visualizing the right time and the right program of maintenance with analyzing the key data of operation