Case study
RM TOHCELLO CO., LTD.
Project | Proyek BCP & Langkah Penghematan Energi |
---|---|
Location | Pabrik Itako / Ibaraki / Jepang |
Industry / Sector | Pabrik produksi film kemasan (pembuatan dan penjualan film kemasan dan lembaran busa yang digunakan untuk makanan, minuman, kebutuhan sehari-hari, bahan pengemas, dll.) |
ISSUE
Tantangan untuk menyeimbangkan stabilitas pasokan listrik dengan efisiensi ekonomi dan ramah lingkungan
Pabrik pelanggan berlokasi di daerah yang tidak memiliki akses listrik komersial yang memadai dan juga rawan terhadap sambaran petir. Oleh karena itu, hingga saat ini, sistem kogenerasi mesin diesel telah digunakan dan dialihkan ke pengoperasian mandiri dalam keadaan darurat untuk menghindari pemadaman listrik dan penurunan tegangan. Dengan berakhirnya kontrak pemakaian mesin diesel, kami mempertimbangkan untuk beralih ke mesin berbahan bakar gas yang bisa menkombinasikan keekonomisan dan keramahan pada lingkungan. Saat memperkenalkan mesin gas, ada kekhawatiran bahwa mesin tersebut kurang mampu mengikuti beban daya listrik selama pengoperasian mandiri dibandingkan sumber listrik komersial. Kemampuan mengikuti beban daya adalah kemampuan untuk memvariasikan keluaran dari mesin sesuai dengan beban daya. Jika kemampuan ini rendah, saat beban daya berfluktuasi secara signifikan dalam waktu singkat, mesin akan mati dan membuat resiko kerugian. Oleh karena itu, perlu adanya peningkatan kemampuan mesin gas dalam mengikuti beban daya dan menstabilkan pasokan tenaga listrik.
SOLUTION
KEY POINTS TO THE SOLUTION
- Berkontribusi pada langkah-langkah BCP dengan memasok listrik secara stabil ke jalur produksi bahkan ketika listrik komersial tidak normal.
- Secara efektif memanfaatkan panas gas buang mesin dan EMS (sistem manajemen energi) untuk meningkatkan efisiensi secara keseluruhan.
- Kurangi emisi CO2 dengan mesin gas ramah lingkungan.
Berkontribusi pada langkah-langkah BCP dengan memasok listrik secara stabil ke jalur produksi bahkan ketika listrik komersial tidak normal
Sistem kogenerasi mesin gas Mitsubishi Heavy Industries (MHI) dicirikan oleh kemampuannya untuk mengamankan tenaga yang stabil bahkan dalam keadaan darurat. Kemudian, untuk mengatasi kekhawatiran bahwa “mesin gas memiliki kemampuan yang lebih rendah dalam mengikuti beban daya listrik dibandingkan sumber listrik komersial, dan terdapat risiko hilangnya daya dalam keadaan darurat,”, kami mengukur beban daya listrik di pabrik pelanggan secara detail. Kami juga melakukan beberapa pengujian menggunakan mesin pengujian. Hasilnya, kami dapat menunjukkan bahwa dengan mengubah spesifikasi mesin dan meningkatkan urutan operasional (langkah dan prosedur pengoperasian), pasokan daya listrik yang stabil dapat disediakan meskipun beban berfluktuasi secara signifikan dalam waktu singkat. Selain itu, kami juga memasang beberapa unit kogenerasi mesin gas untuk menghindari risiko matinya seluruh pasokan listrik jika terjadi kegagalan. Melalui upaya ini, kami berkontribusi terhadap langkah-langkah BCP pelanggan kami.
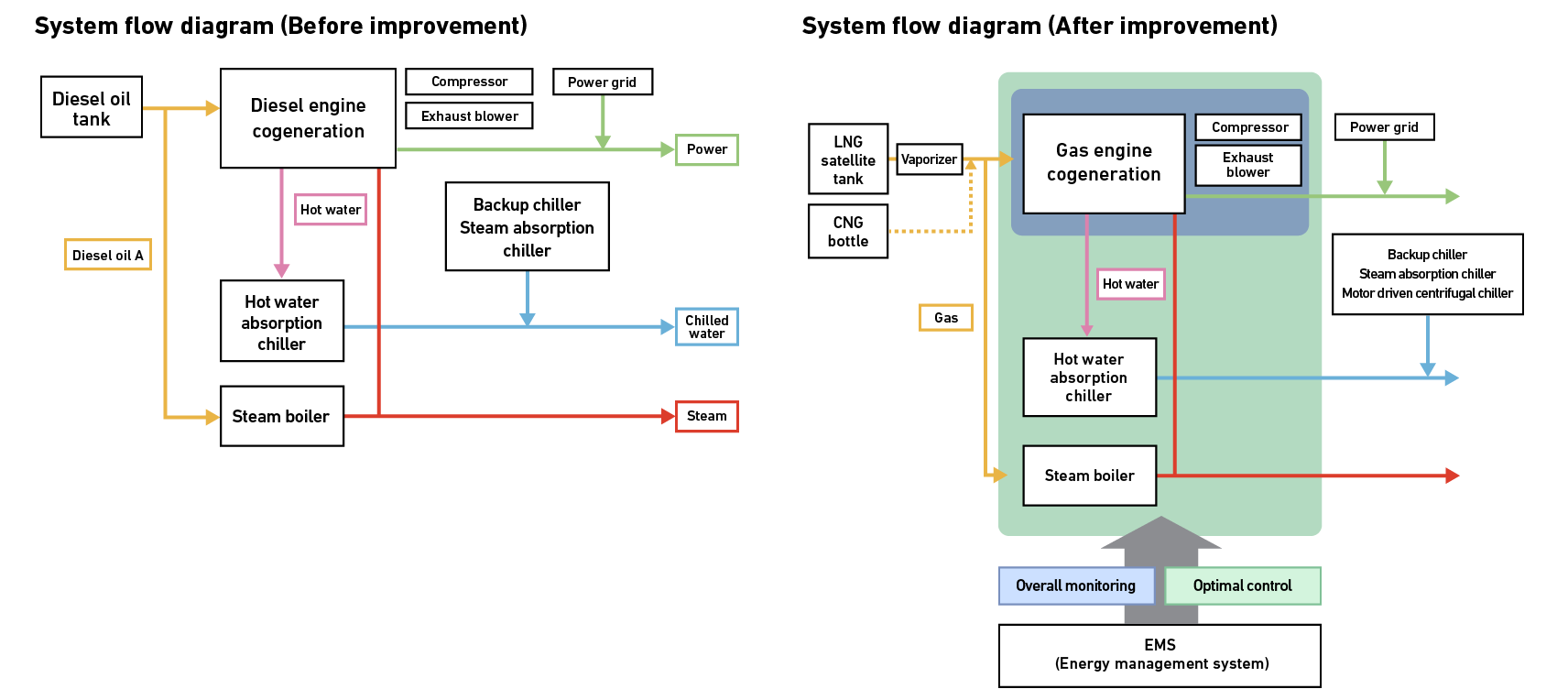
Secara efektif memanfaatkan panas gas buang mesin dan EMS (sistem manajemen energi) untuk meningkatkan efisiensi secara keseluruhan.
Sistem kogenerasi mesin gas MHI menggunakan air pendingin mesin gas (yang dibuang sebagai air panas) untuk chiller dan gasifikasi LNG, sehingga menghasilkan efisiensi system keseluruhan yang lebih tinggi dibandingkan mesin gas pada umumnya. Pada saat yang sama, untuk membuat manajemen energi lebih efisien, sistem manajemen energi (EMS) memvisualisasikan berbagai data seperti volume panas air dingin dan penggunaan udara. Dengan memanfaatkan beberapa fungsi EMS untuk mengontrol kogenerasi mesin gas, kami dapat mewujudkan tingkat penghematan energi yang tinggi dan mengurangi biaya pengoperasian secara signifikan.
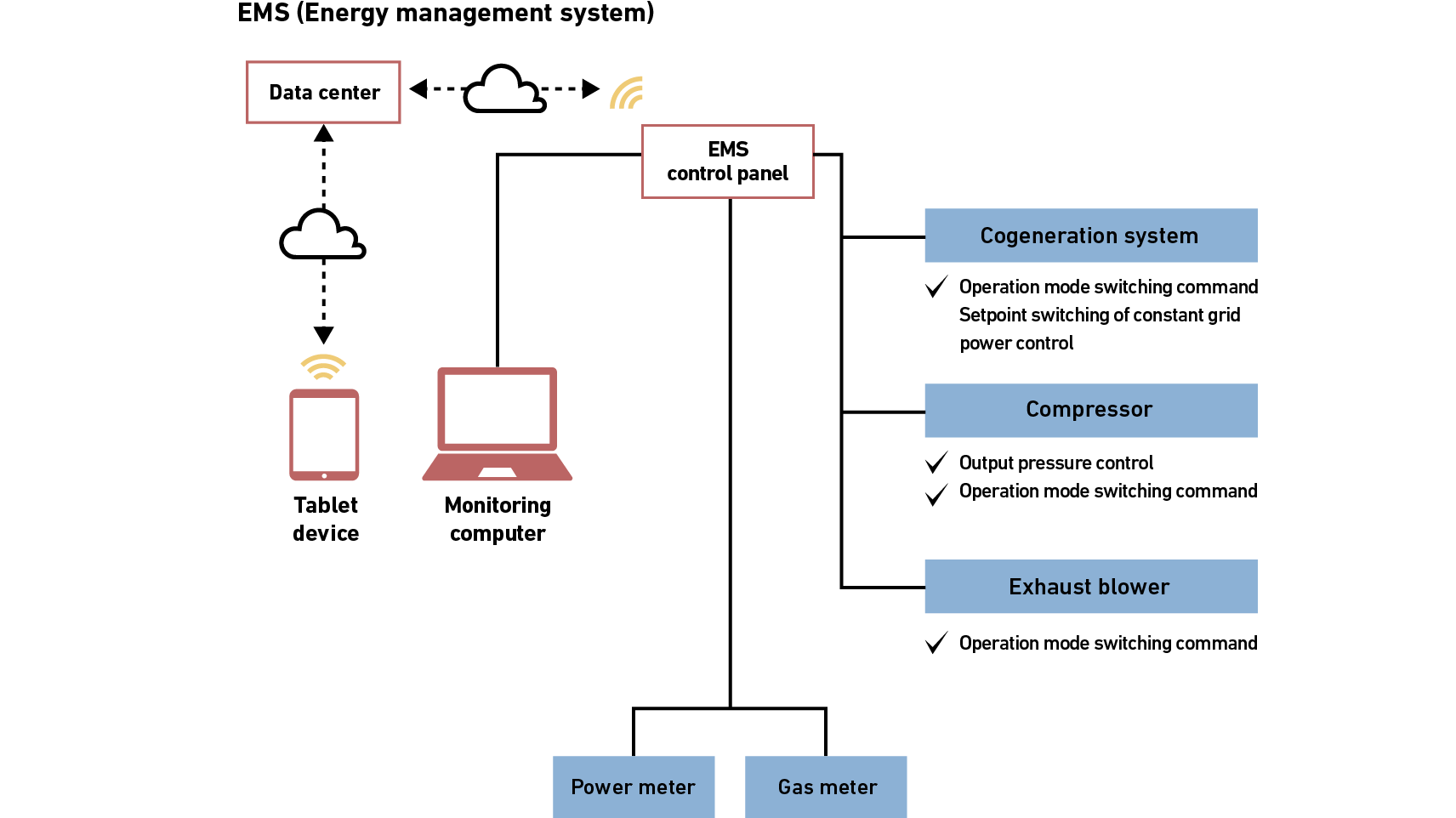
Kurangi emisi CO2 dengan mesin gas ramah lingkungan.
Mesin gas menggunakan gas alam sebagai bahan bakarnya, yang menghasilkan lebih sedikit CO2 dibandingkan mesin diesel sehingga memiliki dampak lebih kecil terhadap lingkungan. Selain itu, sistem kogenerasi mesin gas MHI yang sangat efisien membakar gas dalam kondisi optimal untuk mencapai emisi bersih. Hasilnya, kami berhasil mengurangi emisi CO2 dan NOx (nitrogen oksida).
OUTCOME
- Menyediakan listrik yang stabil bahkan dalam keadaan darurat dan berkontribusi terhadap tindakan BCP
- Penghematan energi dan pengurangan biaya operasional melalui penggunaan sisa panas yang sangat efisien
- Mengurangi emisi gas rumah kaca termasuk CO2
CUSTOMER VOICE
Pabrik Itako terletak di daerah yang sering terjadi sambaran petir, dan sebelumnya sistem kogenerasi mesin diesel dialihkan ke operasi mandiri untuk menghindari penurunan tegangan seketika akibat pemadaman listrik. Saat mempertimbangkan untuk mengganti sistem tersebut dengan sistem kogenerasi mesin gas, muncul permasalahan bahwa mesin gas mengutamakan efisiensi yang tinggi, sehingga dibandingkan dengan mesin diesel, kurang mampu mengikuti beban daya listrik selama pengoperasian mandiri. MHI melakukan pengujian berulang kali menggunakan mesin pengujian, dan dengan mengubah spesifikasi, kami mampu mencapai efisiensi tinggi dan peningkatan kemampuan mengikuti beban daya listrik. Dengan memperkenalkan sistem kogenerasi mesin gas, kami dapat mencapai penghematan energi dan pengurangan CO2 secara signifikan, dan melalui penggunaan subsidi, kami juga dapat mengurangi biaya layanan energi. Selain itu, pengelolaan energi menjadi lebih mudah karena berbagai data dapat divisualisasikan menggunakan EMS. Kami ingin terus berupaya melakukan kegiatan konservasi energi.