Solution
Modifying steam power plants to lower emissions
The global pursuit of the energy transition has generated strong demand for low-carbon and renewable fuel. Yet, thermal power plants still play an important role in maintaining stability of power supplies in many countries around the world. The environmental impact of thermal power plants must therefore be reduced, and Mitsubishi Power has a variety of solutions to do so, including biomass- and ammonia-firing technology as well as solutions to convert existing coal or oil-fired power plants to natural gas.
FEATURES
Making power plants cleaner
By converting to natural gas, CO₂ emissions per kWh will be reduced by 40% compared to coal firing and 30% to oil firing. As natural gas has lower nitrogen content, significant NOx reduction (compared to coal firing) can be achieved with the installation of our low-NOx burner. Furthermore, as natural gas has lower sulfur and ash content, SOx and ash emission will reach nearby zero. Natural gas’ higher ramping rate and better ignition quality also enable greater flexibility and help decrease minimum load on operation, making natural gas-fired power systems more compatible with renewable energy.
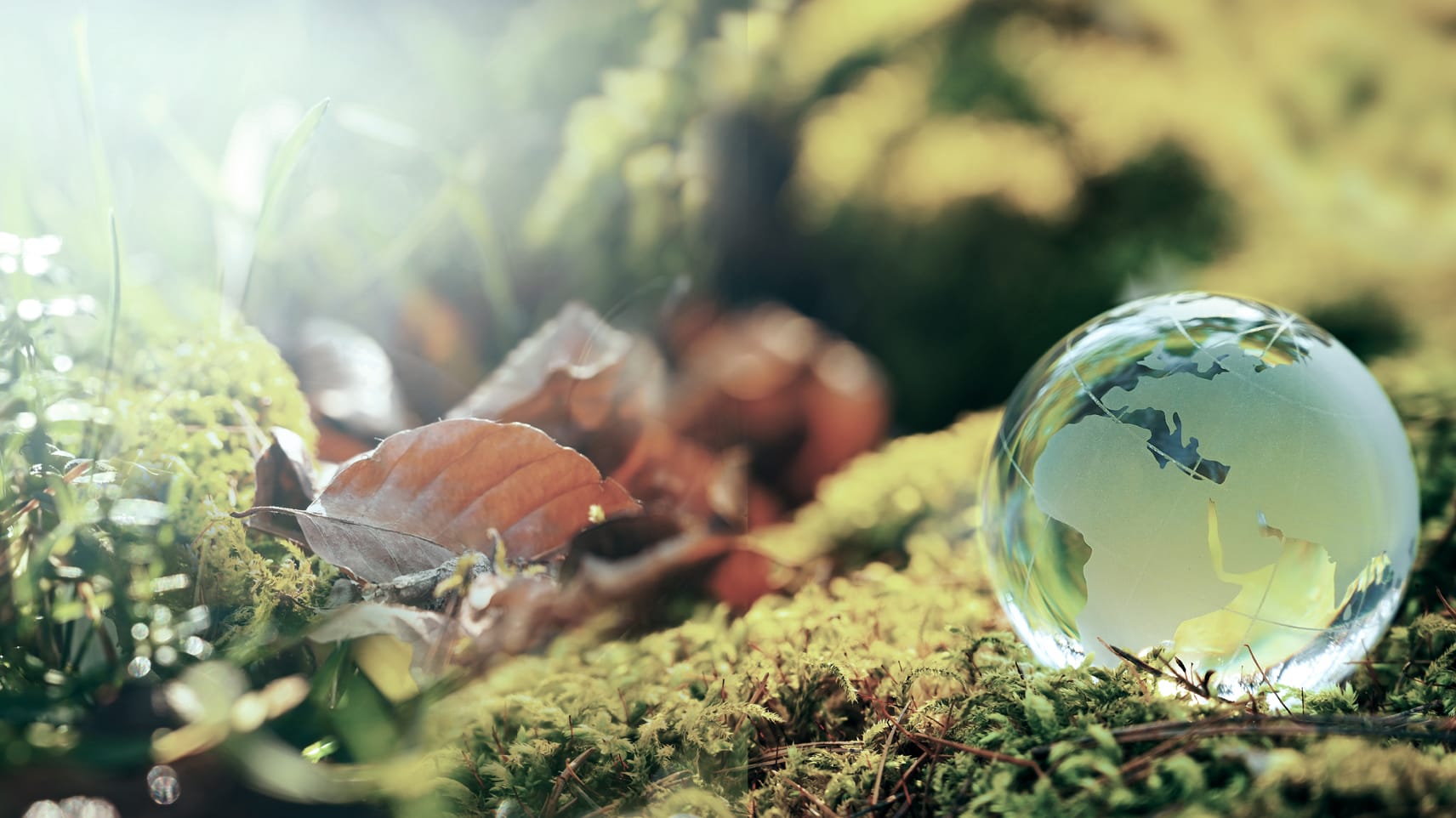
Customizing solutions based on extensive global experience
Fuel conversion retrofit does not mean just a simple burner replacement. Evaluation on how the conversion will affect the entire power plant and all equipment within it is needed. Mitsubishi Power, as a full Engineering, Procurement and Construction (EPC) provider, has more than 5,500 experiences including both opposed and corner firing boilers. We have been designed for different plant conditions such as output, steam flow, and environmental standards. We offer a one-stop solution that meets specific customer requirements and location, including optimizing the features of existing plants:
- Wide variety of proposals available based on the customer’s environmental targets and the features of the existing plant*¹
- Recommendations based on the consideration of the effects by gas conversion for related equipment*²
*¹ Conversion to biomass/natural gas (on its own or cofired with coal) In-furnace NOx reduction, AQCS systems (SCR, EP, FGD, GGH) *² Impact on overall heat balance, existing superheaters, existing air and gas flow system, and existing AQCS systems
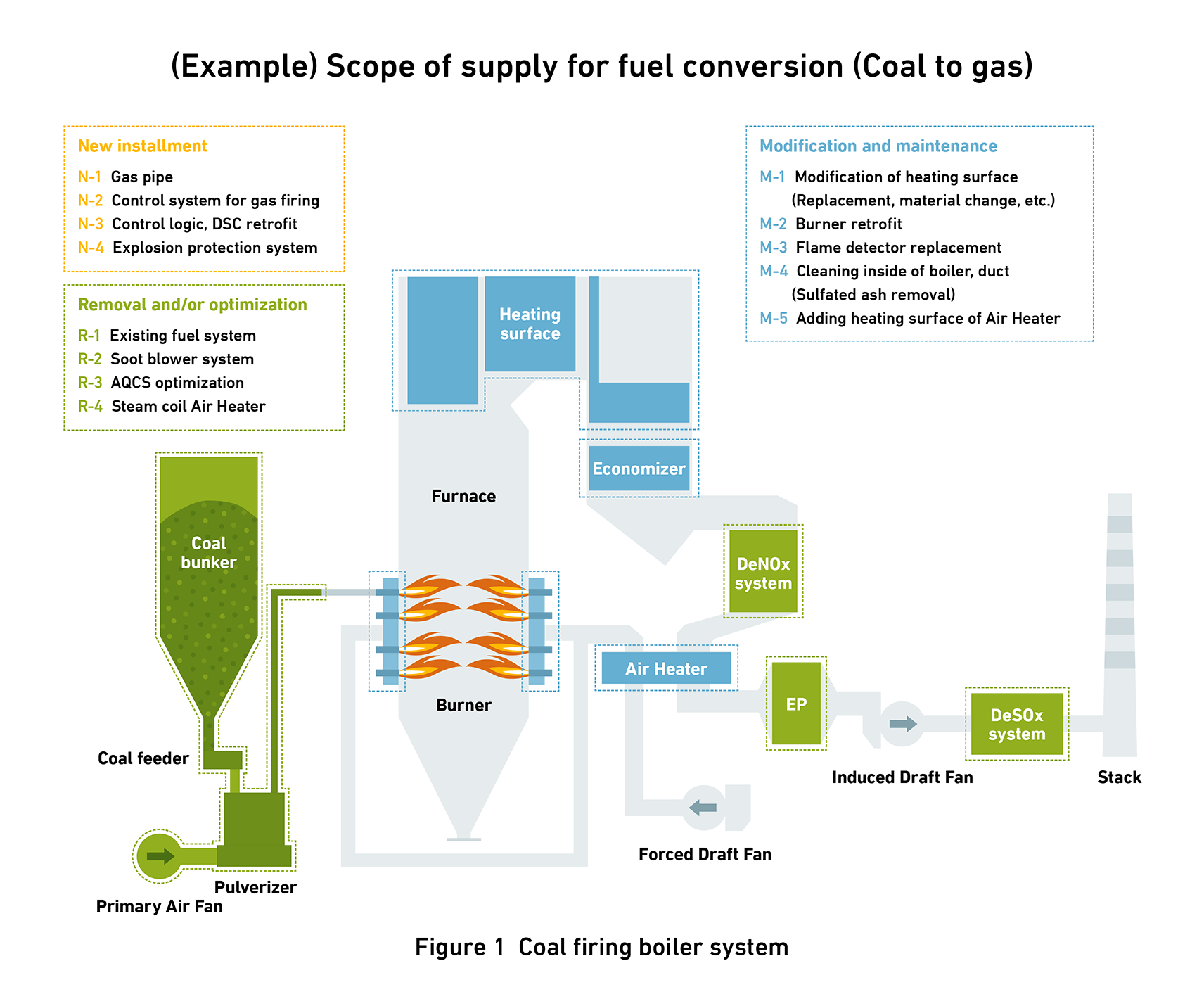
Reducing Operation & Maintenance costs
By converting coal- or oil-fired boilers to gas-fired boilers, customers can achieve the following results:
- Reduction of boiler tube deposits and corrosion due to flue gas, optimizing boiler capacity factor and efficiency and lowering fuel costs as well as maintenance expenditure for the heating surface.
- Reduction of O&M costs due to lifetime extension of existing DeNOx catalysts and reduced ammonia consumption. (Compared to coal firing)
- Reduction of O&M costs for related facilities due to removal of operation and maintenance for existing fuel supply systems and ash cleaning systems.
DOWNLOADS
NEWS
-
Mitsubishi Power to Develop Ammonia Combustion Systems for Thermal Power Plant Boilers -- To achieve optimal combustion characteristics for mixed and single fuel operations --
-
Mitsubishi Power’s Gasification Technology Contributes to Supplying Sustainable Aviation Fuel from Woody Biomass for Regularly Scheduled Flight -- Entrained Bed Gasification Technology Contributing to Decarbonization in Aviation --
-
Mitsubishi Power Receives Turnkey Order for 50MW Woody Biomass-fired Power Generation Facility -- Mitsubishi Power to Coordinate EPC Work for Biomass Facility in Hyuga, Miyazaki Prefecture --
- See more news
FOR MORE INFORMATION
- Links to Mitsubishi Heavy Industries Group’s online media SPECTRA and Mitsubishi Power website.
- Steam Power Plants
- Steam Turbines
- Why we still need natural gas to help us get to net zero