Case study
Industry: Captive thermal power facilities
ISSUE
Transition from natural gas to achieve carbon neutral by 2050
Looking beyond interim targets for 2030, industrial captive thermal power facility owners realize the need for further energy transitions in addition to converting from coal to natural gas. To this end, they are considering hydrogen as the fastest and economical option for a conversion to a clean fuel that realize zero CO₂ emission. Following are some of the considerations for conversion to hydrogen:
- How to make the best use of existing facilities
- How soon will hydrogen be available
- What modifications are needed to use hydrogen as fuel and when will these modifications be available
Given the fact that there is not enough public information on plants running on hydrogen, it is logical that owners should insist on highly reliable equipment with rigorous validation.
SOLUTION
KEY POINTS TO THE SOLUTION
- Validation to enhance reliability for hydrogen utilization
- Minimal system modifications for conversion to hydrogen fuel
- Keeping project schedule as planned
Validation to enhance reliability for hydrogen utilization
One of the challenge to realize hydrogen combustion in gas turbines is its fast combustion speed that may cause flashback; firing backwards against fuel supply. Mitsubishi Power’s gas turbines have a proven track record of firing a wide variety of fuels, including hydrogen-rich fuels, and the company is fully aware of the challenges with hydrogen-firing. We will convert the demonstration facilities, called T-Point 2 located at the Mitsubishi Power Takasago Machinery Works, into the Takasago Hydrogen Park. In the new facility, validation of hydrogen combustion at the grid-connected environment prior to product introduction will be conducted. It will enable us to identify risks or problems in advance and make improvements before delivering the product to our customers. The validation results will be immediately shared with the R&D, design, and manufacturing departments located at the same site so that improvements can promptly be applied to actual products. Mitsubishi Power will continue to demonstrate its high reliability through these sequences, and this approach will be also taken now in hydrogen-fired systems.
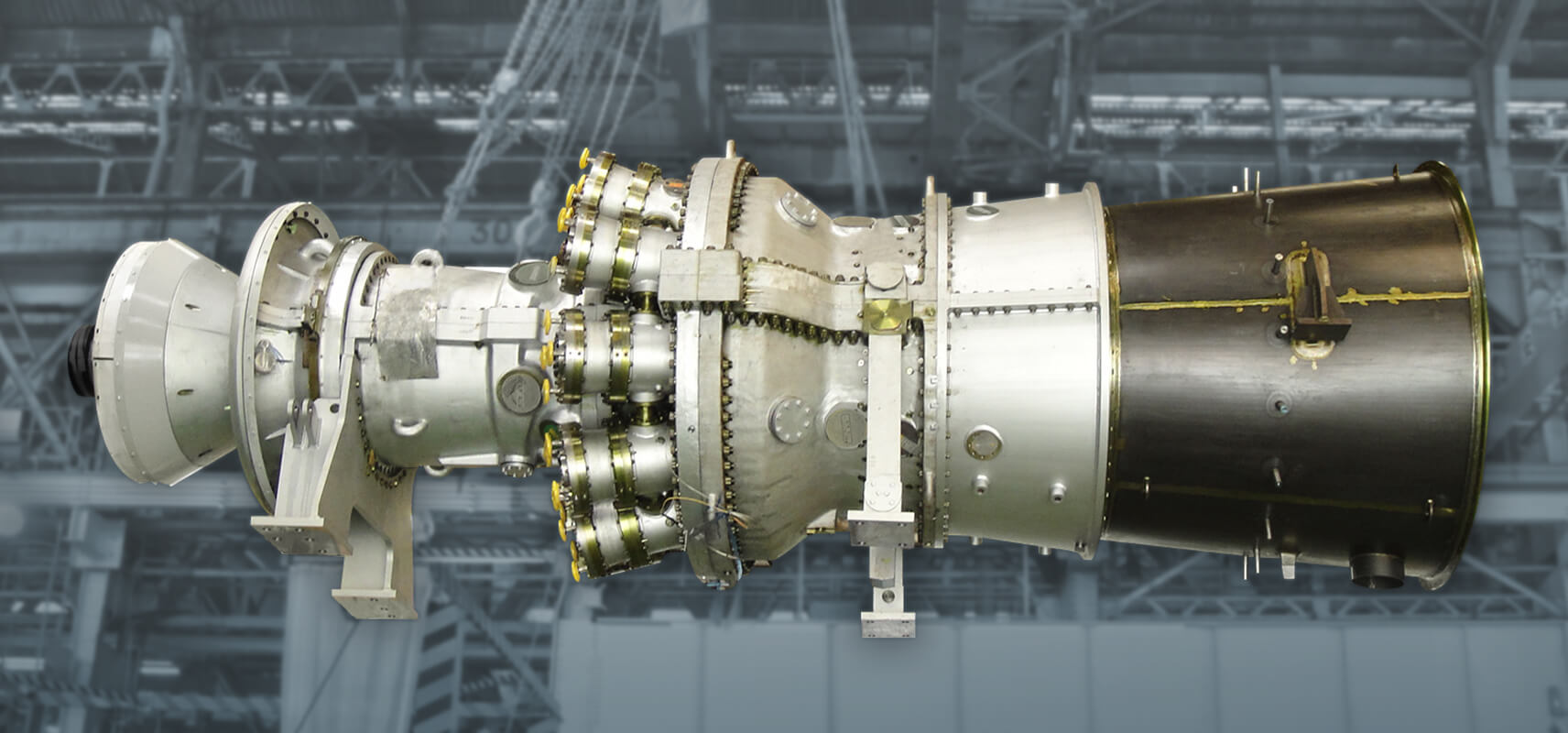
Minimal system modifications for conversion to hydrogen fuel
The major modifications needed to convert natural gas fired gas turbines to hydrogen fired gas turbines are:
- Replacing the combustor
- Modifying the fuel system
- Adding a hydrogen gas system
Existing natural gas-fired facilities can be used to the maximum extent possible, and the conversion to hydrogen combustion can be accomplished with some additions and modifications, making fuel conversion possible with minimal investment. This is particularly the case as combustors are originally designed to be easily removable for maintenance .
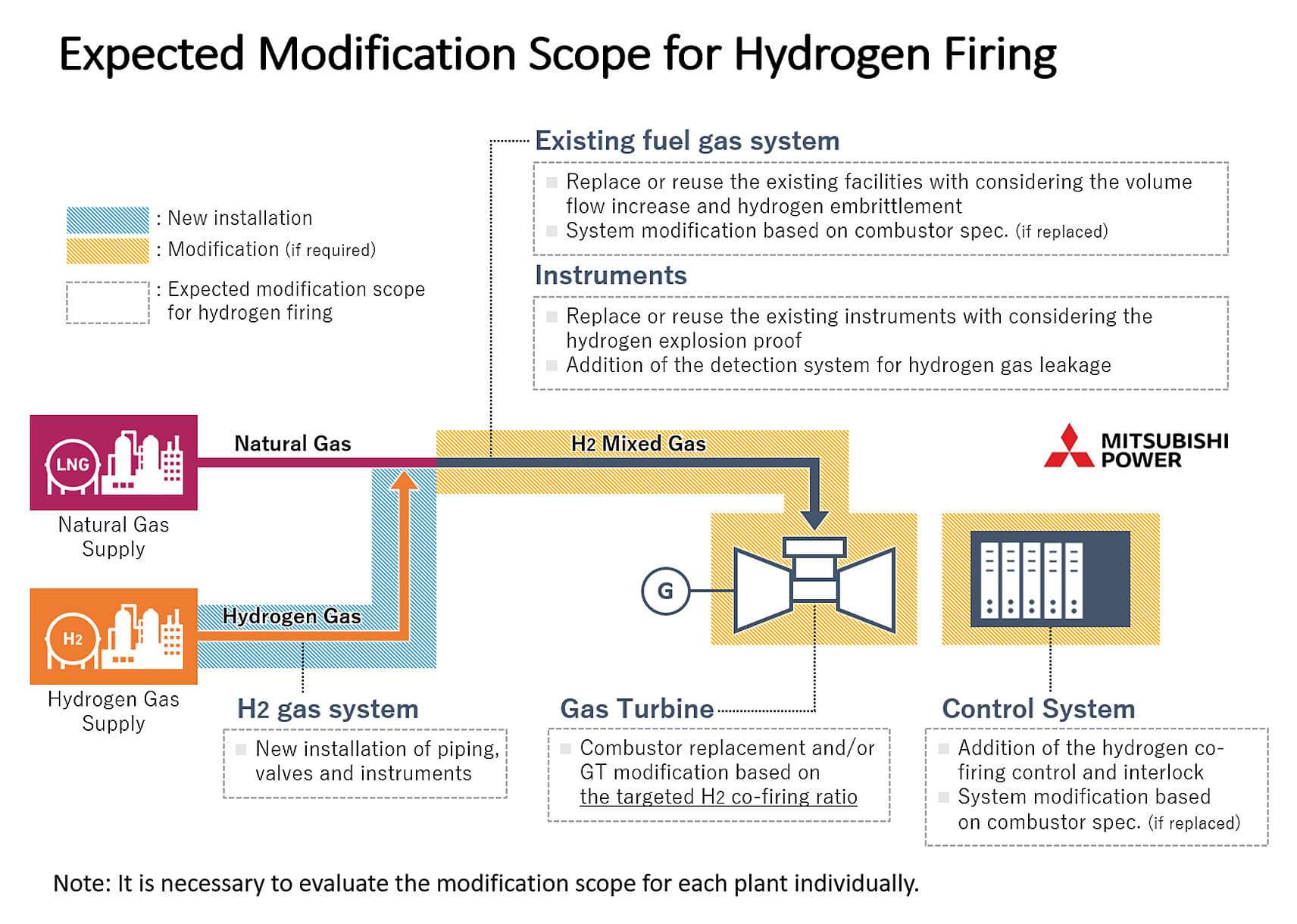
Keeping project schedule as planned
Mitsubishi Power already offers 100% hydrogen-fired with diffusion combustors for H-25 gas turbines. Meanwhile, a high-performance multi-cluster combustor, which has lower NOx emissions than the diffusion combustors, will be installed in an actual H-25 gas turbine at Takasago Hydrogen Park. 100% hydrogen-fired validation test will be completed in 2024. Using this unique approach of validation of the first unit at one’s own manufacturing location, Mitsubishi Power provides high reliability to future installation at customers plants.
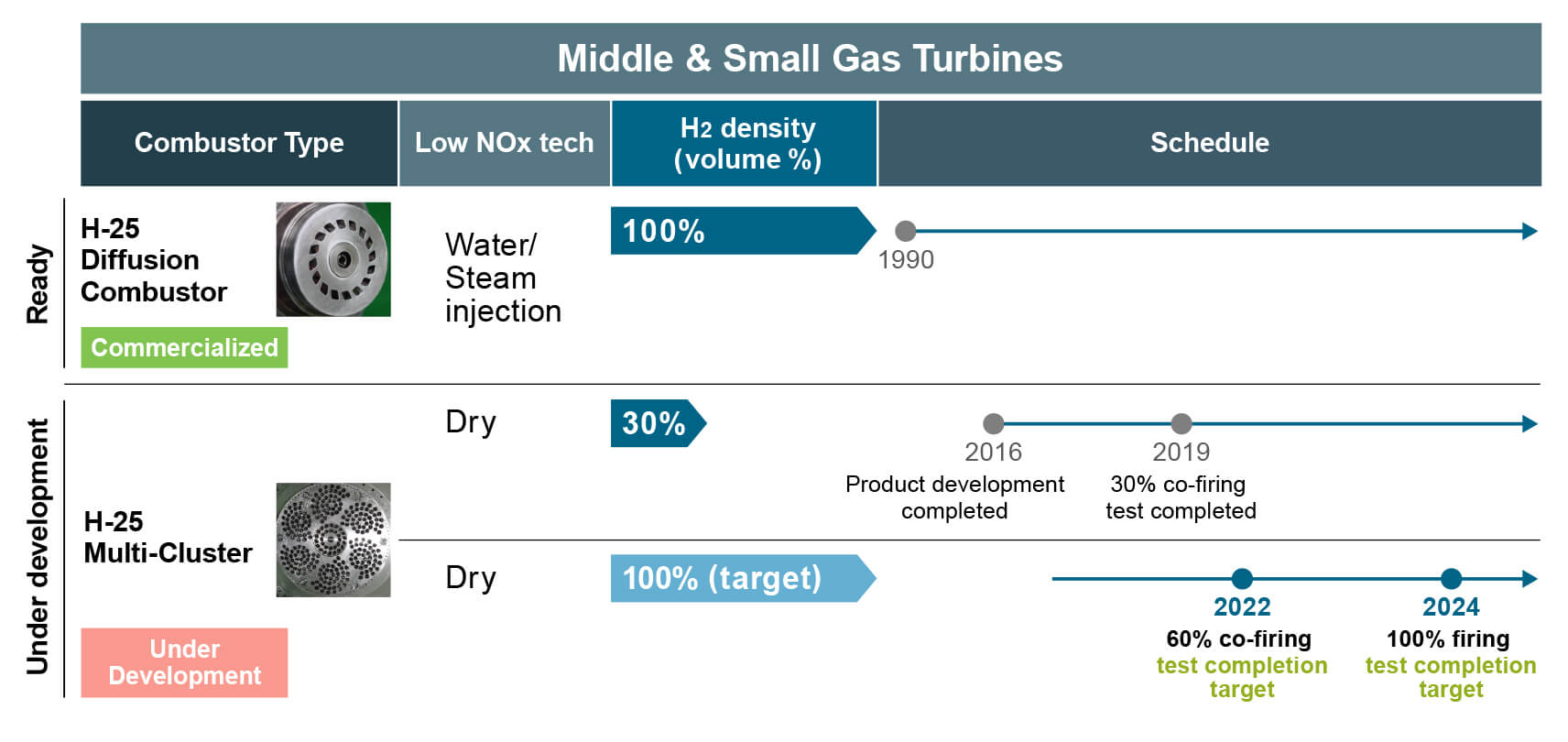
EXPECTED OUTCOME
- Ensure a stable supply of clean energy by shifting to hydrogen-firing which has been validated in demonstration facilities
- Minimizing investment by reducing the modifications to existing power generation facilities
- Provide high confidence level in planned project schedule